Introduction
In recent years, the need for sustainable practices and environmental stewardship has become paramount across various industries. One such sector that has made significant strides in reducing its ecological footprint is the distillery and ethanol production industry. To address the challenges of wastewater management and pollution, a revolutionary solution called Zero Liquid Discharge (ZLD) has emerged. This blog explores the concept of ZLD and highlights the effectiveness of Scaleban technology as a solution in achieving this goal in distillery and ethanol plants.
Understanding Zero Liquid Discharge
Zero Liquid Discharge(ZLD) is an innovative approach to wastewater management that aims to eliminate the discharge of any liquid effluent from industrial facilities. Instead of releasing untreated or partially treated wastewater into water bodies, ZLD systems focus on recovering and reusing all the water produced during industrial processes. The goal is to achieve a closed-loop system where no water is wasted or polluted.
Get in Touch with Us for Zero Liquid Discharge
Challenges in Distillery and Ethanol Plants
Distilleries and ethanol plants generate large volumes of wastewater due to the nature of their operations. This wastewater, known as vinasse, contains high concentrations of organic matter, residual sugars, and other pollutants. If not properly treated, it can pose significant environmental risks, including water pollution and depletion of oxygen in aquatic ecosystems. Traditional treatment methods are often inadequate in effectively handling the complex composition of vinasse, necessitating a more advanced and sustainable solution.
Scaleban Technology
Scaleban technology has revolutionized the achievement of Zero Liquid Discharge in distillery and ethanol plants by Utilizing CPU-treated water as a makeup to cooling towers.
Get in Touch with Us for Zero Liquid Discharge
In Distillery plants, wastewater is generated from multiple sources, hence the requirements of setting up huge CPU plants, RO plants and MEE & ATFD has become the need for achieving ZLD through conventional means.
Scaleban enables the utilization of distillery wastewater successfully as makeup to cooling towers, hence completely eliminating the requirement of setting up RO & MEE.
The remaining concentrated brine coming out of cooling towers can be used for ash quenching, dust separation or in the existing MEE of Spent wash which undergoes crystallisation . This final step enables the recovery of valuable salts and minerals present in the wastewater. By carefully manipulating temperature and concentration levels, these substances can be separated and collected. The recovered salts and minerals hold potential for reuse within the facility or can be sold, providing an additional revenue stream for the distillery or ethanol plant.
Scaleban technology maximizes the efficiency of wastewater treatment while simultaneously minimizing environmental impact. This innovative solution not only ensures compliance with stringent regulations but also offers financial benefits through resource recovery and potential revenue generation. The adoption of Scaleban technology in distillery and ethanol plants represents a significant step towards sustainable and responsible industrial practices
Benefits of Scaleban Technology
Implementing Scaleban technology offers several advantages for distillery and ethanol plants. Firstly, it enables the complete elimination of liquid effluent discharge, ensuring compliance with stringent environmental regulations. Secondly, the recovered CPU water can be reused within the facility Cooling towers reducing the reliance on freshwater sources and minimizing overall water consumption. Additionally, the recovery of valuable salts and minerals provides an opportunity for cost savings and revenue generation.
UN Sustainable Development Goals
UN Sustainable Development Goal 6: Clean Water and Sanitation:
The implementation of Scaleban technology in distillery and ethanol plants aligns with UN Sustainable Development Goal 6, which focuses on ensuring clean water and sanitation for all. By achieving Zero Liquid Discharge, these industries significantly reduce their water consumption and minimize the release of untreated or partially treated wastewater into water bodies. Through the advanced treatment processes of membrane filtration, evaporation, and crystallization, Scaleban technology enables the recovery and reuse of water resources within the facilities. This approach contributes to sustainable water management by reducing the strain on freshwater sources and promoting responsible water consumption practices.
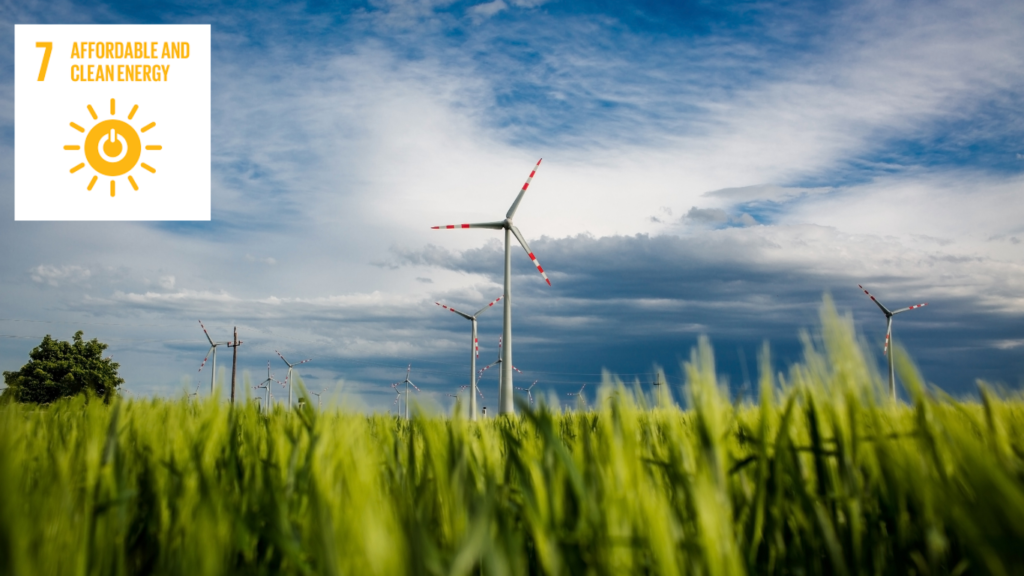
UN Sustainable Development Goal 7: Affordable and Clean Energy:
Scaleban technology also supports UN Sustainable Development Goal 7, which aims to ensure access to affordable, reliable, sustainable, and modern energy for all. By incorporating evaporation and crystallization processes, the technology harnesses the thermal energy of the wastewater to drive water vaporization and mineral separation. This energy recovery mechanism reduces the reliance on external energy sources, making the treatment process more efficient and cost-effective. Additionally, the recovery of valuable salts and minerals from the concentrated brine presents opportunities for resource monetization, creating an additional revenue stream for distillery and ethanol plants. Through the adoption of Scaleban technology, these industries can contribute to the transition towards a cleaner and more sustainable energy future while ensuring their operational needs are met.
Conclusion
Zero Liquid Discharge, facilitated by Scaleban technology, presents a viable and sustainable solution for distillery and ethanol plants to address their wastewater management challenges. By implementing this innovative approach, these industries can significantly reduce their environmental impact while improving water resource management. The benefits of ZLD, such as compliance with regulations, water conservation, and the recovery of valuable resources, make it an attractive choice for forward-thinking businesses seeking to prioritize sustainability and long-term profitability. With the adoption of Scaleban technology, distillery and ethanol plants can set a benchmark for responsible and eco-friendly operations in the larger industrial landscape.